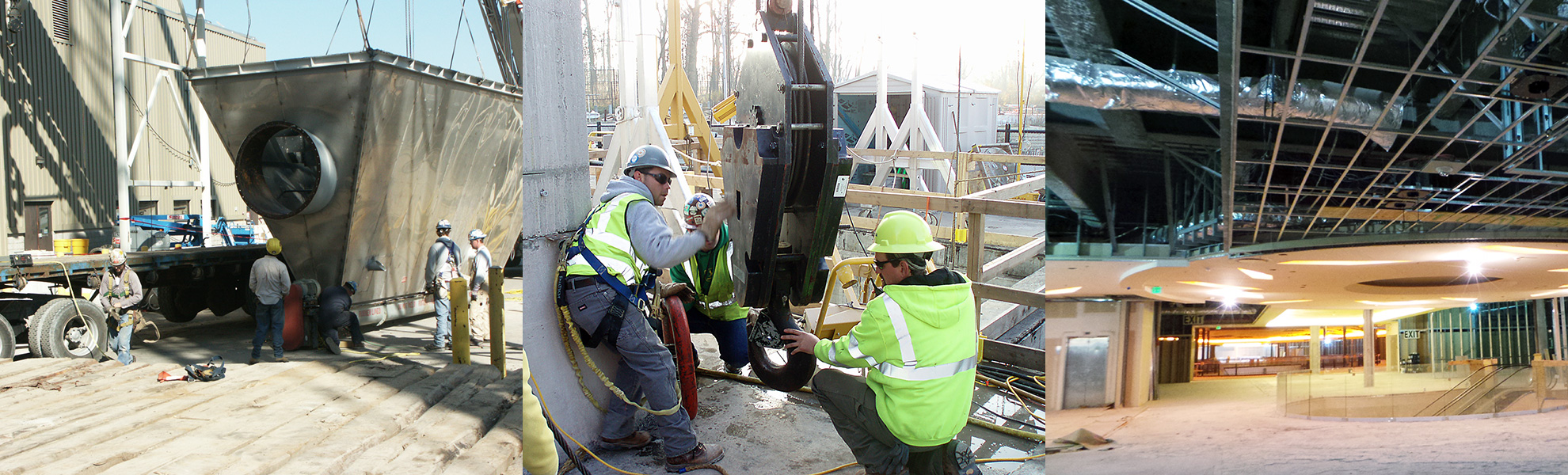
Wooden Rooftop Water Tanks: Familiar Fixtures of NYC Skyline
Wooden rooftop water tanks are common features of the New York City skyline. The barrel-like, cone-roofed structures first appeared on city rooftops in the late 19th century, and have been an integral part of New York’s water system ever since.
After the Civil War, New York flourished and tall buildings began to crop up around the city. Because New York is built on shallow bedrock, natural water pressure was too low to raise water to the upper stories of these buildings, so rooftop tanks were introduced. Nowadays, electric pumps that are commonly used in U.S. cities are impractical with New York’s aged infrastructure, and rooftop tanks still provide the ideal solution to the city’s water needs.
The first rooftop water tanks were constructed by barrel makers, and even today about 99% are still made of wood. Steel tanks can cost up to four times more, require far more maintenance, and can impart a metallic taste to the water. Wood has natural insulating properties, keeping water cool in summer and preventing freezing in winter.
There are only two companies that currently build water tanks in New York. These “tankmen”, as they’re known, can construct the body of a tank in as little as two hours, setting boards in place using only a hammer and a rope. Tank walls, made from either cedar or California redwood and held together by cables or “hoops”, leak when first filled. As the wood becomes soaked, it swells and the tank becomes impermeable. No sealant is necessary.
The average rooftop water tank is about 10-12 feet high and stores 5,000 to 10,000 gallons of water. As water is used and levels drop, a pump is triggered and the tank is refilled. Water used for drinking and bathing is siphoned from the top of the water. Water in the lower half, where sediment settles, is reserved to fight fires.
Tank maintenance is a straightforward process that takes about six hours and causes little inconvenience to building residents. Water is drained and the interior is scrubbed with a chlorine solution. The tank is refilled, a second chlorine solution is added, allowed to soak, then flushed out. Switches are lubricated, holes are caulked, and hoops are tightened. The supporting structure also requires maintenance – mostly scraping and painting – on a regular basis. Rooftop water tanks have an average lifespan of 20 to 25 years, and when particularly well-maintained tanks can last as much as 30% longer.
Though rooftop water tank technology was developed more than 150 years ago, New York’s reliance on them is not expected to change any time soon. The method is simple, inexpensive, effective, and well-suited to existing city infrastructure. R. Baker & Son has been involved in a number of renovation and demolition projects in which rooftop water tanks have been relocated or dismantled. Though they look like relics of the past, rooftop tanks will undoubtedly remain a customary fixture of the New York cityscape for many years to come.
About R. Baker & Son All Industrial Services
R. Baker & Son All Industrial Services, a Service-Disabled Veteran-Owned Small Business (SDVOSB) in business since 1935, is a premier specialized contractor operating in the United States, Canada and Puerto Rico, with over one hundred employees and an exemplary safety record (we have been directly involved in four sites that received VPP OSHA Safety Awards). R. Baker & Son is financially strong, with bonding capabilities over $10 million. Capabilities include industrial and commercial demolition, rigging, machinery- and plant-moving, dismantling, decommissioning, plant and equipment relocation, interior demolition, selective demolition, warehousing, wrecking and razing, millwright, plant reconfigurations, heavy rigging, salvage, environmental services, remediation, decontamination, abatement, and investment and asset recovery..
Demolition, wrecking and razing, rigging, millwright, plant reconfigurations, heavy rigging, Service-Disabled Veteran-Owned Small Business / SDVOSB, salvage, dismantling, decommissioning, plant and machinery moving, building demolition, riggers, environmental services, remediation, decontamination, abatement, interior demolition, investment and asset recovery.
R. Baker & Son All Industrial Services
1 Globe Court
Red Bank, NJ 07701
Phone: 732-222-3553
Fax: 732-450-0311
Facebook: facebook.com/Demolition.Rigging
Full News Archive
2025
- Healthcare Demolition: ICRA Protocol & Clean Environments
- Lean Construction: Optimize Demolition, Rigging & Dismantling Projects
- Rigging Services for NYC and NJ: Offsite Storage & Asset Management
- Rigging: A Complete Guide to Safety, Equipment, and OSHA Standards
- Construction Safety Stand Down: History and Purpose
- The Future of Rigging & Demolition in NY & NJ
- Rigging NYC and NJ - Most Iconic Structures with Expert Precision
- Why Telescopic Cranes Are Essential in Rigging Work
- Expert Rigging and Maintenance for Industrial Mixing Tanks
- Vertical Water Curtains: The Future of Dust Control in Urban Implosions
- Precision Planning in Construction Demolition
- Precision MEP Install at a South Jersey Manufacturing Facility
- Precision Demolition: R. Baker & Son's Advanced Equipment & Techniques
- Comprehensive Guide to Plant Relocation: Planning for Success
- How Virtual Reality is Changing Riggers Training
- Chemical Bursting: The Silent Revolution in Concrete Demolition
2024
- Demolition and Rigging: A Half Century of Safety Innovation
- Safety Through Dialogue: The Critical Role of Toolbox Talks
- The Critical Importance of Safety Investment in Construction
- Understanding the Difference Between Lowest Price and Best Price
- Accelerated Project Timelines with R. Baker BIM Laser Scans
- Building a Safer Environment: The Power of Positive Safety Habits
- R. Baker Seamlessly Rigging and Replacing Old Equipment
- R. Baker & Son Hospital Wing Interior Demolition
- R. Baker & Son's Rigging Expertise Shines in Pharma Expansion
- R. Baker & Son Comprehensive Equipment Management Strategy
- Expert Rigging: Meticulous Planning for Safe Lift Projects
- Efficient Rigging and Equipment Setup: Planning and Collaboration
- Eco-Friendly Solutions for Dismantling, Demo & Decommissioning
- Selective Demolition and Rigging at Process Plant
- Rigging Success: Chiller & Cooling Tower Installation at Jersey Hospital
- Celebrating a New Year from R. Baker & Son
- Maximizing Your Demolition Project - Tips to Define Scope|Budget
2023
- Industrial Demolition in NYC: A Look at the Process and Impact
- Rigger's Guide to Machine Skates - Role in Heavy Load Movement
- Seven Key Questions Clients Want to Know About Demolition
- Interior Demo of Old School for Conversion to Residential Units
- Versa Lift
- Emergency Call Shows - Value of the Right Rigging Equipment
- Structure Support is Critical on Demolition Projects
- R. Baker & Son Saves Client Over $100K on Rigging Project
- Hats Off To Mechanics
- Intensive Plant Cleanup - Rigging, Disassembly, Reassembly
- R. Baker & Sons Demo Experience to Find the Best Plan
- Top Rigging & Demo Performance on Front Stage and Backstage
- Safety is a Mindset at R. Baker & Son
- Disassemble and Relocate Water Treatment Systems
- Planning for Dust, Noise, and Vibration on Demo Projects
- Machinery Moving and Assembly Project
- Rigging and Assembling Test Equipment-NJ Processing Facility
- Concrete Slab X-Rays Enable Accurate Cutting and Drilling
2022
- R. Baker & Son Wins 3 Highwire 2022 Platinum Safety Awards
- Rigging and Assembly in New Storage and Maintenance Facility
- Plant Machinery Updates and Replacements
- Understanding Physics and Construction are Vital in Demolition
- Slips, Trips and Falls According to OSHA
- Spreader Beams a Top Choice for Rigging Stability and Safety
- Important Safety Basics for Interior Demolition Projects
- Tool and Equipment Tracking - Crane Rigging
- Cleanup of Demolition Dust, Dirt, Silica, and Particulates
- Auger and Centrifuge Rigging Project
- University Cooling Tower Dismantling Project
- Rigging, Dismantling & Demolition Project Safety
- Baker Performs Multi Heat Exchanger Changeout
- Preconstruction Services or Precon
- Asset Recovery: Refurbished Parts and Equipment in High Demand
- Weekend Standby Generator Replacement
- R. Baker & Son: Rigging Project Consultation
- Interior Demolition: Epoxy Floor Removal
- Chemical Pilot Plant Demolition Project
- Decommissioning and Dismantling of HVAC Equipment - Pharma
- History of the Versatile Skid Steer Loader
- Qualified Rigging Contractor In Writing
2021
- Organization Mobilization on a Project
- Every Demolition Project Needs a Quality Control Plan
- Rigging & Assembly Made Efficient by Color Coding
- Demolition, Asset Recovery, and the Supply Chain
- Innovation in Rigging Helps Preconstruction
- Safe, Successful Demolition Projects Start with Good Planning
- Hurricane Ida Ground Stabilization
- We are a NYC Minority and Women-owned Business Enterprise
- Architectural Salvage During Demolition
- Rigging Plan Consulting and Estimating
- Interior Demo - Making Way For New Manufacturing Facility
- Zero Punch List Approach to Demolition
- R. Baker & Son Process Tank Repair Project
- Selective Demolition in Medical School Building
- R. Baker & Son Provides a Wide Range of Environmental Services
- Emergency Generator Repair at NJ Hospital
- Requirements of Selective Demolition in Healthcare Facilities
- R. Baker & Son Demo Team Completes Partial Plant Demolition
- Rigging and Anchoring Heavy Machinery and Equipment
- Baker Completes Selective Demolition Project on Christmas Eve
- 3D Rigging Using Building Information Modeling
- Stainless Steel Tank Rigging Project Saved by Plan B
- Taking On Diverse Tasks on Renovation and Construction Projects
2020
- Crane & Rigging Operations and Safety During Winter
- Demolition Safety: Structural Shoring and Bracing
- Emergency Warehouse Demolition Brooklyn
- Rigging & Assembly Teams Install Pharma Fill Line
- Planning a Rigging Project with BIM
- Expert in NYC Curtain Wall Dismantling and Demolition
- Interior Demo: Mid-Project Changes Save Time and Money
- Site-Specific Safety Plan - SSSP
- R. Baker Workers Trained In Heat Related Illness
- Tank Rigging Project - Large Food Processing Plant
- The Skid Steer Loader, Workhorse of the Demolition Industry
- Baker Handles Pharma Rigging Project with TLC
- Innovative Approach to Clean Air on Demo Project
- Proper Radio Communication on Construction Sites
- Demolition and Closing the Gap on Project Delays
- Rigging and Setting the Final Pieces of Process Equipment
2019
- Quick Mobilization on Interior Demolition Project
- Rigging and Installing Prefabricated Skids
- Rigging Team Assists in Green Roof Installation
- Everyone Loves Demolition Day - R. Baker and Son
- Successful Plant Relocation Project - Master Plan
- Storing and Rigging Specialized Bio-Equipment for New Laboratory
- Reuse and Value Engineering - Save Money on Projects
- Rigging and Assembly on HVAC Upgrade Project
- What are the Fundamentals of Rigging
- Why CPR and First Aid Training is Critical in Construction
- Successful Hospital Renovation Project
- Demolition Contractor: Earning and Keeping Our Great Reputation
- Rigging Setting the Final Pieces of Process Equipment
- Demolition Project Goes Underground
- Copper Recycling Offsets Dismantling Project Costs
- CUP Multi-Phase Selective Demolition Project: Demo by Color
- Rigging Safety Guidelines and Procedures
- R. Baker Salvages Fixtures for Reuse on Plant Consolidation
- Safety Planning for Rigging and Demolition Projects
2018
- Rigging Process Equipment Narrow Shaft
- Demolition Equipment Maintenance SOP
- Module Rigging and Installation
- Challenging and Dangerous Duct Demolition
- Counting Cranes to Forecast Construction Growth
- Demo Protection on Pharmaceutical Project
- Plant Relocation Specialists - R. Baker and Son
- Baker Works w/ MEP Engineers to Accelerate Plant Relocation
- Fire Protection Requirements in Demolition
- Rigging Equipment - Plan of Control
- Confined Space Construction Rule
- Scrap Metal Prices Are On The Rise
- Virtual Reality The Future of Crane & Rigging Training?
- Rigging, Hoisting & Heavy Equipment Careers
- Substantial Cost Savings in Space Repurposing Project
- Demolition: A Little Ingenuity Goes a Long Way
2017
- Substation & Mechanical Selective Demolition: Out With the Old
- Colossal Claw Revolutionizes Rigging of Sunken Oil Rigs
- Kosciusko Bridge Demolition UPDATE
- Innovative Plan in Manhattan High Rise Project
- Experienced in Cleanroom Demolition
- Tower Crane Luffing Jib - Rigging Requirements
- Coming to a Demolition Site Near You: ZeroG Tool Arm
- Cleanroom Demolition - Preventing Particulates
- Ground-Penetrating Radar (GPR) and Demolition
- Environmental Cleanup in Demolition and Rigging
- Dust, Noise, Vibration and Odor
- Demolition by Implosion an Impressive Sight to See
- Fortune 100 Selective Demolition
- IRAs Seven Rs for Asset Recovery
- Demolition: What's Your Approach?
- Hazardous Noise in Rigging and Demolition
- NYCs Busy Kosciuszko Bridge to be Imploded Summer 2017
- What is a Critical Lift - Crane and Rigging
- Rigging Near Overhead Powerlines
2016
- Compact Boom Lifts Fit Through Standard Doorways
- Rigging of Modular Prefab Pharmaceutical Plants
- Dismantling Clean and Green with R. Baker and Son
- Hydraulics: The Force Behind Rigging & Demolition
- Surgical Industrial Dismantling
- 3D Rigging and Routing Plans, BIM
- Construction Machinery at NJ's Diggerland
- Safe Conditions - The Demolition Environment
- Inspection Of Rigging Equipment
- Demolition and Lead-Based Paint: Safe Practices for Cutting Steel
- National Stand Down for Fall Prevention
- Demo Project Bid Leveling Sheets Can Make All the Difference
- NYC Demolition a Wellspring of Architectural Salvage
- Calculating Interior Demolition Costs
- Total Demolition, Stadium-Style
- Industrial Rigging A Wind Turbine
- Demolition Teams Critical in Disaster Response
- Demolition Contractors Are Creators
- Construction Drones - Providing Eyes In The Sky
2015
- Preserving Old Buildings For Nostalgia
- Tank Farm Dismantling Project - New Jersey
- Expert in Transporting Oversize Loads
- BIM on Plant Relocation Projects
- Skilled Trade Workers: The Shortage Continues
- Understanding Basic Structural Physics Key to Safe Demolition
- The Intricacies of Building Implosion
- What is Buried in Concrete is an Important Part of Demolition
- Remote Control Demolition Machines
- Demolition Live on Construction Cameras
- Costa Concordia Cruise Liner Capsized
- Rubble Trouble New York Video Game
- The R. Baker and Son Outrigger - June 2015
- Rigging - R. Baker & Son has the Skill
- The Complexity of Plant Relocation Projects
- Rigging the Great Pyramid of Giza
- Warehousing Facilities - Protecting Your Investments
- Corporate News - Indoor Warehouse Facility
- Various Demolition Methods and Types
- Helicopter Rigging An Effective Alternative
- The March 2015 Outrigger - An R. Baker & Son Newsletter
- More States Offering Plant Relocation Incentives
- Selective Demolition: Punch Lists Leave Lasting Impressions
- Metal Recovery and Recycling - Construction Debris
- Excavation of Contaminated Soil
- Sky Cranes, Tower Cranes, What Do You See?
- The Outrigger News - December 2014
- In Need Of Qualified Experienced Riggers
2014
- Dismantling Electrical Systems
- Demolition in a Confined Space
- Utility Safety During Demolition
- Brokk Demo Machines on Pharma Project
- Demolition of Uranium Facility, Once the Largest Building in U.S.
- Crane Load Charts and Capabilities
- Selective Demolition and Preserving History
- Largest Container Cranes and Rigging
- How It Works: BIM in Rigging & Demolition
- September 2014 Issue of "The Outrigger"
- Mold Remediation on Demolition Projects
- Pre-Project Rigging and Demolition Safety Measures
- R. Baker & Son Equipment and Machinery Moving
- Demolition Permit Approvals Show Steady Increase in New York
- Qualified Riggers vs. Certified Riggers: What is the Difference?
- Fluorescent Bulb Recycling and Mercury
- Outrigger Newsletter June 2014
- The Complexities of Plant Relocation
- Brownfield Sites and Land Revitalization
- Man Baskets in Rigging, Demolition, and Dismantling
- New York City Demolition Waste
- Mobile Crane Vs Fixed Crane Safety
- Hard Hats - Safety Equipment and PPE
- R. Baker & Son: Rigging Safety Guidelines
- Check Out - The Outrigger Newsletter, March 2014
- Supporting Women, Minority, and Veteran-Owned Businesses
- Expert Professional Rigging Services
- R. Baker & Son Partners on Numerous OSHA VPP Star Projects
- R. Baker & Son Top-Rated by ISNetworld
- EPAs Website Simplifies Compliance
- Use of Robotic Equipment Expanding in Demolition Industry
2013
- R. Baker & Son Selected as ENR Top 600 Specialty Contractor
- First Aid Kits & Construction Safety
- Nuclear Power Plant Decommissioning
- R. Baker & Son: Dust Suppression and Control
- Ruby Baker and the History of R. Baker & Son
- Wooden Rooftop Water Tanks: Familiar Fixtures of NYC Skyline
- Demolition Vibrations Used to Study Earthquakes
- Clean Projects Keep an Eye on the Environment
- The Future of High-Rise Demolition in NYC
- The Difference Between Riggers and Millwrights
- Plant Relocation: Working with a Multi-Phased Master Plan
- Asset and Investment Recovery in the Modern Market
- Demolition, History and Wrecking Balls
- NYCs Lesson in Preservation: Demo of the Original Penn Station
- R. Baker & Son the Clear Choice for NYC Demolition
- Keeping a Construction Jobsite Clean
- 3D Laser Scanning Excellent Tool for Project Planning
- Specialized Carriers & Rigging Association
- Smart Phones and Construction Apps
- 79th Annual Investment Recovery Seminar
- March 2013 Rigging and Demolition Newsletter
- Interior Demolition and the Work Environment
- Crane and Rigging Fundamentals
- OSHA Safeguarding Workers for Over Forty Years
- Air Casters Provide Simple Rigging Solutions
- Statue of Liberty Renovation Project
2012
- Tricky Job With A Very Aggressive Schedule
- Building Information Modeling Tools
- Borescope Use In Construction and Demolition
- Three Industrial Classes For Hard Hats
- A Tale of Two Projects - Red Bank, NJ
- September 2012 Rigging and Demolition Newsletter Now Available
- ENR Magazine Ranked R. Baker #1 Demolition/Wrecking Contractor
- Clients Expect Total Care in Plant and Equipment Relocation
- Investment Recovery Reduces Project Costs
- Bringing Safety Home According to OSHA
- R. Baker & Son - Handling the Largest of Projects with Total Care
- June 2012 Rigging and Demolition Newsletter Now Available
- R. Baker & Son Recognized by Skanska for Safety Commitment
- World Trade Center Transportation Hub Project H&M Wall Demolition
- Dust, Noise and Vibration During Demolition and Rigging
- Brownfields Go Green with Renewable Energy
- R. Baker & Son is ISNetworld Rated A
- Baker Rigging Services Make Room for Space Shuttle Enterprise
- Join Us at INTERPHEX 2012 May 1-3 2012 at Javits Center NYC
- Safety a Priority - R. Baker & Son Maintains VPPPA Membership
- R. Baker & Son March 2012 Outrigger Newsletter Available
- Proud Sponsor of Patty-Joe Goodwin Undefeated Snowboarder
- Dust, Noise and Vibration During Demolition
- R. Baker & Son Proud Members of the SC&RA
2011
- Demolition and Decommissioning Planning Document Available
- An Interview with David S Baker - President of R. Baker & Son
- R. Baker & Son Rigs Russian Space Capsule at Intrepid Video
- R. Baker & Son in ACT Magazine Sept 2011
- Come Visit R. Baker & Son at INTERPHEX 2011 in Puerto Rico
- Slideshow Of Rigging Performed at National 9 11 Memorial Museum
- The Rising : Rebuilding Ground Zero - Discovery Channel Video
- 5000 pounds of Babbit Scrap Metal For Sale
- Video of FDNY Ladder 3 Lowered into 911 Museum by Baker
- LEED: Maximizing Your Rating Points
- R. Baker & Son Leading Demolition Company in North America 2011
- R. Baker & Son June 2011 Rigging Demolition Newsletter Available
- Water Tower Demolition Experts
- R. Baker Completes Fast Paced Pharmaceutical Rigging Project
- R. Baker & Son Video of Dustboss in Action
- Used Equipment Sale DC Motor Generators and Electrical Equipment
- R. Baker & Son Renews NJ Public Works Contractor Registration
- March 2011 Rigging and Demolition Newsletter Available
- Visit R. Baker & Son Booth at INTERPHEX 2011 March 29 - 31
- R. Baker & Son Renews VPPPA Membership for 2011
- The Missing Work Scope In Mission Critical
2010
- Lock Out Tag Out Safety Practices
- Exhibiting at 2010 POWER-GEN International Tradeshow
- R. Baker & Son Dec 2010 Rigging and Demolition Newsletter
- OSHA New Final Rule on Cranes and Derricks
- Hard Hat News Sept 2010 Article Features R. Baker & Son
- R. Baker & Son in Equipment Today Magazine September 2010
- R. Baker & Son Makes 2010 World Demolition Awards Shortlist
- Sept 2010 Rigging and Demolition Newsletter Available
- R. Baker & Son Ranked #1 Demolition- Wrecking Contractor 2010
- R. Baker & Son Is Your Best Industrial Contractor Choice
- NDA Publishes High Reach Demolition Safety Document
- New NYC Dept of Buildings Safety Registration
- Website of R. Baker & Son Updated to Highlight Services
- R. Baker & Son June 2010 Outrigger Newsletter Now Available
- Dun & Bradstreet Reaffirms R. Baker & Son 3A3 Rating
- New Puerto Rico Business Development Manager
- R. Baker & Son Establishes Better EMR Safety Rating
- Demolition and Rigging Newsletter March 2010 Now Available
- Visit R. Baker & Son at the INTERPHEX Puerto Rico 2010
- R. Baker & Son Featured on Facility of the Year Awards Website
- R. Baker & Son Featured in Crane Hot Line Magazine
- R. Baker & Son Rigging and Demolition Blog
- R. Baker & Son Highlights Rigging Services Photo Album
- Plant Relocation and Reconfiguration Services
- R. Baker & Son Featured in Hard Hat News Jan 15 2010
- Highlights Industrial Demolition Contractors Services in NJ
2009
- R. Baker Featured on Building Design & Construction Website
- December 2009 Outrigger Newsletter Available From R. Baker & Son
- R. Baker & Son is a Proud Member of the VPPPA
- Follow R. Baker & Son All Industrial Services on Facebook
- Highlights of Interior Demolition Contractors Services
- R. Baker and Son Veteran Owned and Operated
- Equipment Today Features Demolition Project by R. Baker and Son
- Baker Highlights Demolition Services in NJ
- Petrochemical Plant Dismantlement Project in The News
- R. Baker & Son Completes Demolition Project for Con Edison
- R. Baker & Son Highlights Recent Safety and Industry Awards
- Global Rigging Services and Machinery Moving
- R. Baker & Son Ranked in Inc. 5000 Fastest Growing Companies 2009
- Baker on NY Constructions 2009 Specialty Contractor List
- Demo and Remediation Project in NYC Featured in Magazine
- BioPharm Plant Relocation in NJ Safely Completed
- Preserving the Past Article Features R. Baker & Son
- Hard Hat News - Story on R. Baker and Son Demolition Project
- Construction Equipment Guide Story on Dismantling Project
- R. Baker & Son Dismantles Cooling Towers at Active Facility
- How to Think Globally and Act Locally
- R. Baker and Son Safety Record Featured in Hard Hat News
- Historic Preservation of Coastal Defense Gun Battery
- R. Baker Named as a Leading Demo Company in North America
- Yankee Atomic Nuclear Plant Dismantling Project
- R. Baker & Son Rigging Project Featured in Hard Hat News
- R. Baker Contributes to Pharmaceutical Client Winning FOYA
- R. Baker & Son Featured in Site Prep Magazine
- Pre-Engineered Modular Construction by R. Baker & Son
- R. Baker & Son All Industrial in the LEED on GREEN Since 1935
- R. Baker & Son Wins EBJ Business Sustainability Achievement Award
- R. Baker & Son Announces 5th Year of Non-Recordable Incidents
- To All of Our Valued Employees, Subcontractors and Customers
- R. Baker & Son Featured in American Recycler Magazine
2008
- Rigging and Machinery Relocation Completed
- R. Baker & Son Featured in Blasted - Show on Science Channel
- R. Baker & Son Featured On Environmental Expert Website
- C&D Recycling Magazine Features R. Baker & Son
- R. Baker & Son Featured in Construction Equipment Guide
- Baker Listed in Directory of Building Deconstruction Companies
- Plant, Machinery and Facility Relocation Contractors Services
- R. Baker & Son Featured in C and D Recycling Magazine
- Nationwide Building Demolition Contractors Services
- R. Baker & Son Listed as 2008 Top Specialty Contractor
- Highlights Water Tower Demolition Services
- Completed Relocation and Installation of Intrepid Brass Propeller
- Completes Critical Installation of Generator for Private Client
- R. Baker & Son Completes Selective Demolition of LNG Vaporizers
- R. Baker on Cover of American Cranes and Transport Magazine
- Constructioneer Magazine Features Baker Demolition Project
- Service Highlight - R. Baker & Son
- Building Demolition Contractor Services - New Jersey
- R. Baker & Son Makes Quick Work of Fast Food Project
- Awarded Large Rigging and Relocation Project in New York City
- Baker Celebrates 73rd Year in Business
- Large Hospital Demolition Completed by R. Baker and Son NYC
- R. Baker & Son Maintains 3A2 D&B Rating
Recent News
Healthcare facilities present some of the most challenging environments for interior and selective demolition projects, where maintaining a sterile, contamination-free environment is absolutely...
Many R. Baker clients have adopted and use the lean construction process on their projects, the list includes most pharmaceutical companies, energy companies, manufacturing of all kinds along with...
For rigging projects in New York City and New Jersey, access to secure offsite storage and asset management is a crucial component of rigging, setting, and assembly operations,helping accommodate...
Rigging is one of the most critical operations in heavy industry, and at R. Baker & Son, we specialize in safe, compliant lifting with the right equipment, planning, and OSHA-certified practices....
The Construction Safety Stand Down is an annual event aimed at raising awareness about safety in the construction industry, particularly focusing on fall protection. This initiative serves as a...
The Evolving Landscape of Heavy Industrial Services in NYC & NJ R. Baker & Son stands as a cornerstone in the industrial services sector, with a profound legacy rooted in decades of...
For 90 years, R. Baker & Son has been a cornerstone of rigging services in New York and New Jersey, expertly undertaking complex lifting, moving, and safeguarding operations for some of the...
It is remarkable how innovation and technology continue to change and improve construction equipment. Manufacturers have evolved to create machinery that serves multiple purposes at job sites. A...